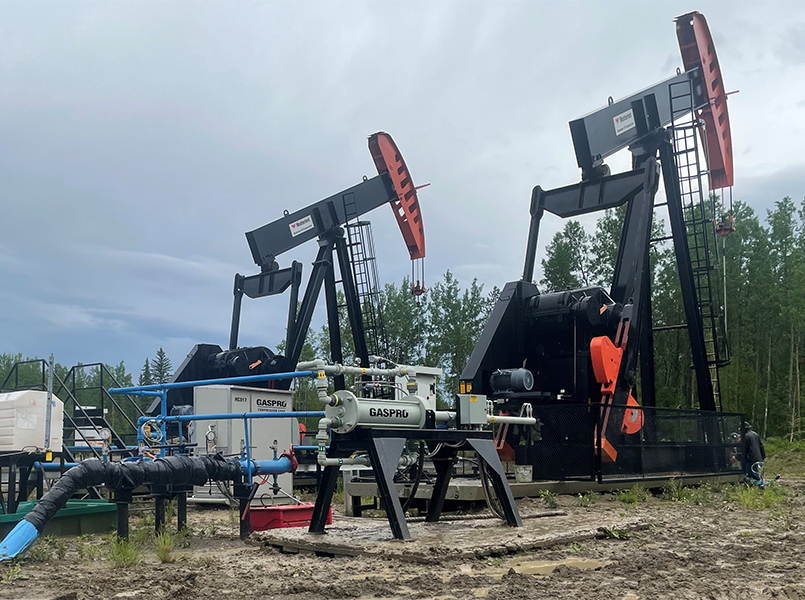
The oil and gas industry relies on advanced technologies to efficiently extract, process, and transport crude oil and natural gas. At GasPro Compression, we specialize in manufacturing innovative equipment, including hydraulic compressor machines, designed to meet the complex demands of this dynamic sector.
This article will cover the intricacies of hydraulic compressors, their types, applications, and why GasPro Compression is a trusted name in the industry.
What is a Hydraulic Compressor?
A hydraulic compressor is a mechanical device that increases the pressure of gases or liquids by reducing their volume. These machines play a critical role in various oil and gas processes, from vapour recovery to pipeline operations. Compact yet powerful hydraulic compressor machines are the backbone of efficient energy management.
Key features of hydraulic compressors:
- Compact Design: Ideal for installations with space constraints.
- High Efficiency: Designed to operate under low energy consumption while achieving high-pressure differentials.
- Versatile Applications: Suitable for gas well boosting, vapour recovery, and other essential operations.
Hydraulic compressors are used in scenarios requiring reliable performance, even under challenging conditions. At GasPro Compression, we design equipment that stands the test of time while ensuring optimal efficiency.
The Types of Hydraulic Compressors
Hydraulic compressors are broadly categorized into positive displacement compressors and dynamic compressors. Each type serves unique operational purposes, and choosing the right one is vital for achieving efficiency and cost-effectiveness.
Positive Displacement Compressors
Positive displacement compressors operate by trapping a specific volume of gas or liquid and compressing it by reducing its volume. This category includes two primary designs: reciprocating and rotary compressors.
Reciprocating Compressors
Reciprocating compressors are widely used for their ability to handle varying volumes and pressure levels.
Single-stage reciprocating compressors:
- Compress gas in a single stroke.
- Suitable for low-pressure applications.
- Are commonly used in smaller operations requiring moderate compression.
Two-stage reciprocating compressors:
- Compress gas through two stages, offering higher pressure capabilities.
- Ideal for applications requiring high-pressure output and efficiency.
Rotary Compressors
Rotary compressors are characterized by rotating mechanisms that compress gases. These compressors are further divided into two subtypes:
Rotary vane compressors:
- Use rotating vanes to compress air or gas.
- They are known for their durability and ability to handle a range of pressure levels.
Rotary screw compressors:
- Utilize two counter-rotating helical screws.
- Efficiently compress gas in distinct suction, compression, and discharge phases.
Dynamic Compressors
Dynamic compressors operate differently by using kinetic energy to compress gases. These compressors are ideal for high-flow, continuous operations.
Axial flow compressors:
- Use multiple rotating blades to achieve high compression rates.
- Commonly used in large-scale industrial operations with high volume requirements.
Centrifugal compressors:
- Employ a diffuser to slow and cool incoming gases, transforming kinetic energy into static pressure.
- Compact, reliable, and capable of producing oil-free air.
- Requires minimal maintenance, making them a cost-effective solution.
Applications of Hydraulic Compressor Machines
Hydraulic compressors have diverse applications in the oil and gas industry, ensuring efficiency, sustainability, and improved economics.
Vapor Recovery
Recover volatile gases that would otherwise be vented or flared, reducing environmental impact and maximizing resource utilization.
Gas Well Boosting
Enhance well output by compressing casing gas, improving productivity and profitability.
Pipeline Operations
Maintain steady gas flow and pressure in pipelines, ensuring uninterrupted natural gas transportation and other resources.
Offshore Installations
Compact and lightweight hydraulic compressors are ideal for space-constrained offshore platforms, providing reliable performance under demanding conditions.
Refining and Processing
Facilitate the refining and processing of crude oil into valuable by-products, such as gasoline and plastics.
At GasPro Compression, we design hydraulic compressor machines tailored to these critical industry applications.
How Do You Select the Right Hydraulic Compressor Machine?
Choosing the right hydraulic compressor involves evaluating several key factors:
- Application Requirements: Determine whether you need a machine for high-volume, continuous flow (dynamic compressors) or variable load operations (positive displacement compressors).
- Flow Rate and Pressure: Assess the required volume of gas or liquid flow and the desired pressure levels for your specific use case.
- Space and Size Constraints: Consider the available space for installation, especially for offshore and compact facilities.
- Maintenance and Longevity: Opt for a compressor with durable components and low maintenance requirements to minimize operational downtime.
- Cost Efficiency: Balance initial investment with long-term operational savings, including energy efficiency and maintenance costs.
GasPro Compression provides expert consultation to help you identify the most suitable hydraulic compressor machine.
Advantages of GasPro Hydraulic Compressors
At GasPro Compression, we specialize in providing advanced hydraulic compressors engineered for reliability, performance, and efficiency. Our commitment to excellence ensures that each machine we deliver meets industry standards and exceeds our clients’ expectations.
Exceptional Durability
GasPro hydraulic compressors are built using the highest-quality materials and precision manufacturing techniques.
- Designed for Harsh Environments: These machines are engineered to withstand extreme industrial conditions, including high-pressure operations, temperature fluctuations, and corrosive environments.
- Long Operational Life: Our compressors are built for longevity, reducing the need for frequent replacements and downtime.
- Rugged Construction: Reinforced designs ensure reliable performance in offshore installations, refineries, and remote field nodes.
Outstanding Energy Efficiency
Energy consumption is a critical concern in industrial operations, and GasPro compressors are optimized to deliver maximum efficiency:
- Minimal Energy Waste: Innovative compression mechanisms reduce power usage while maintaining consistent performance.
- Sustainability: By optimizing energy input, our compressors help clients meet sustainability goals and lower their carbon footprint.
- Cost-Effective Operation: Efficient energy use translates into significant savings over the life of the equipment.
Custom Solutions for Unique Needs
No two operations are the same, and GasPro recognizes the importance of tailored solutions:
- Flexible Designs: We work closely with clients to customize compressor specifications that meet their precise requirements.
- Scalable Options: Whether you need a compact unit for a small application or a large-scale solution for high-volume demands, we’ve got you covered.
- Consultative Approach: Our team of experts provides end-to-end support, ensuring that your compressor seamlessly integrates into your operations.
Environmentally Friendly Operation
As industries move towards greener solutions, GasPro compressors are designed to support environmental sustainability:
- Gas Recovery Systems: Our equipment captures gas that would otherwise be vented or flared, reducing greenhouse gas emissions.
- Pollution Mitigation: By efficiently compressing and managing gases, our machines help clients adhere to stringent environmental regulations.
- Eco-Friendly Design: Materials and components are selected to minimize environmental impact during production and operation.
Significant Cost Savings
GasPro hydraulic compressors are engineered to deliver financial advantages in both the short and long term:
- Low Maintenance: Durable components and streamlined designs minimize the need for frequent servicing, reducing maintenance costs.
- Extended Service Life: The longevity of our compressors lowers the total cost of ownership.
- Improved Operational Efficiency: By reducing energy consumption and downtime, our machines help clients achieve greater profitability.
- Return on Investment: Clients benefit from a high ROI due to reduced operational expenses and enhanced productivity.
Enhanced Safety and Reliability
GasPro understands that safety and reliability are paramount in industrial settings:
- Fail-Safe Features: Our compressors include built-in safeguards to prevent system failures and ensure consistent performance.
- Reliable Operation: Even in demanding conditions, GasPro compressors maintain stable output, reducing the risk of operational interruptions.
- Compliance with Standards: All equipment adheres to industry regulations, providing peace of mind to our clients.
Contact GasPro Compression Today
If you’re looking for state-of-the-art hydraulic compressor machines, GasPro Compression is here to meet your needs. As a leading provider of compressor packages in Canada, we are committed to delivering solutions that enhance efficiency and reliability across the oil and gas industry. Contact us today to request a proposal or learn more about our products and services.