Two-Stage Reciprocating Compressors
The 2-stage reciprocating compressors from Quincy. Download Brochure or Contact Us now to learn more.
15 BHP – Two Stage
Quincy Compressor
Make: Quincy
Model: QRNG 325
Type: Reciprocating
Min / Max Speed: 400-900 RPM
Suction: 1 psi – 30 psi
Max Discharge: 500 psi
Flow: 0.75 e3m3/d – 2.5 e3m3/d
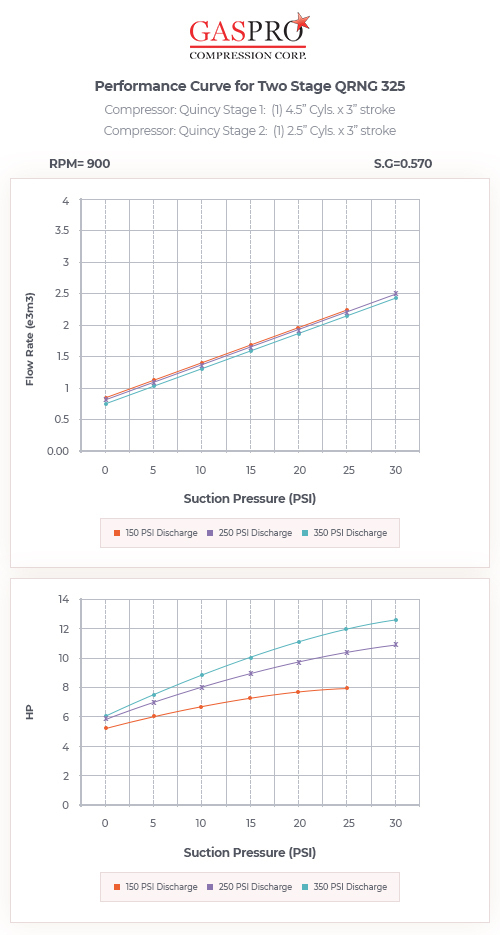
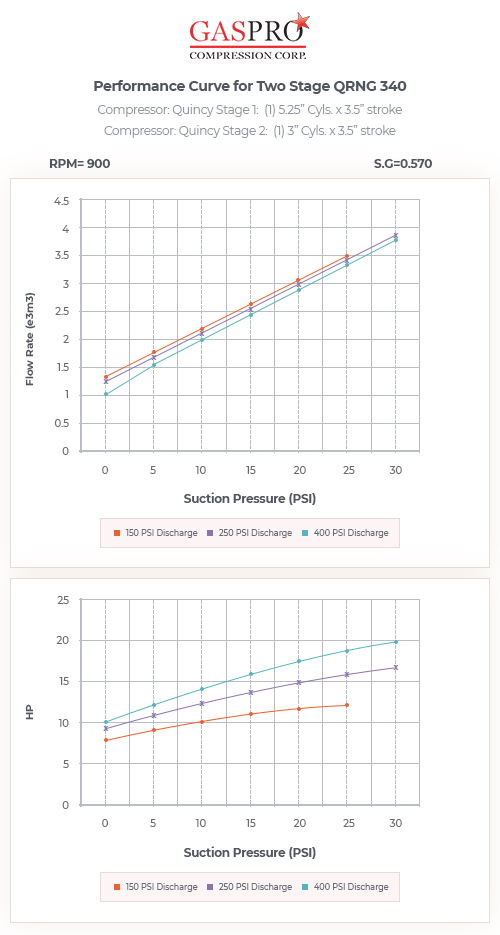
20 BHP – Two Stage
Quincy Compressor
Make: Quincy
Model: QRNG 340
Type: Reciprocating
Min / Max Speed: 400-900 RPM
Suction: 1 psi – 30 psi
Max Discharge: 500 psi
Flow: 1.0 e3m3/d – 4.0 e3m3/d
25 BHP – Two Stage
Quincy Compressor
Make: Quincy
Model: QRNG 350
Type: Reciprocating
Min / Max Speed: 400-900 RPM
Suction: 1 psi – 30 psi
Max Discharge: 400 psi
Flow: 1.1 e3m3/d – 4.75 e3m3/d
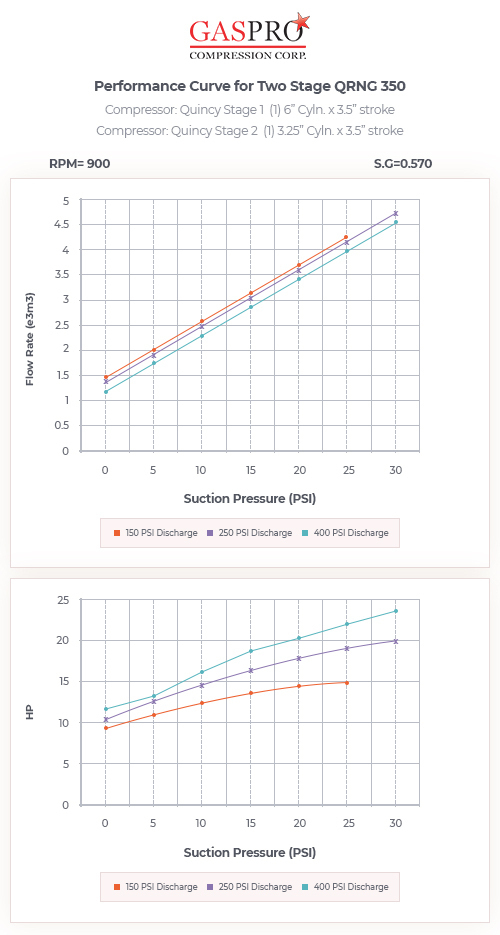
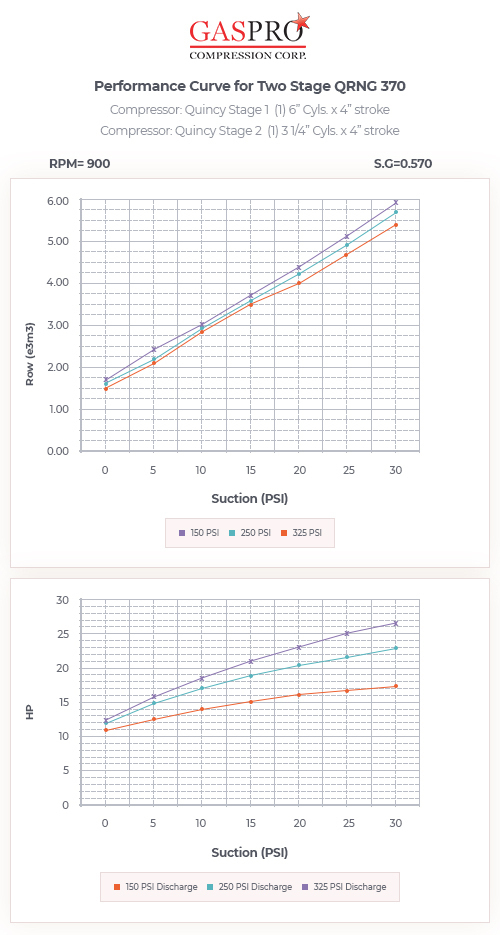
30 BHP – Two Stage
Quincy Compressor
Make: Quincy
Model: QRNG 370
Type: Reciprocating
Min / Max Speed: 400-900 RPM
Suction: 1 psi – 30 psi
Max Discharge: 400 psi
Flow: 1.5 e3m3/d – 6.0 e3m3/d
40 BHP – Two Stage
Quincy Compressor
Make: Quincy
Model: QRNG 5120
Type: Reciprocating
Min / Max Speed: 400-940 RPM
Suction: 0 psi – 20 psi
Max Discharge: 325 psi
Flow: 3.0 e3m3/d – 8.7 e3m3/d
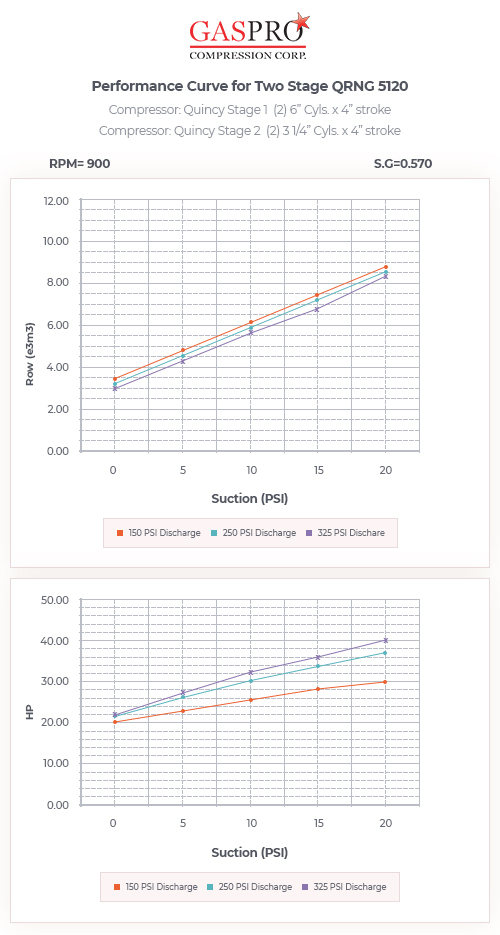
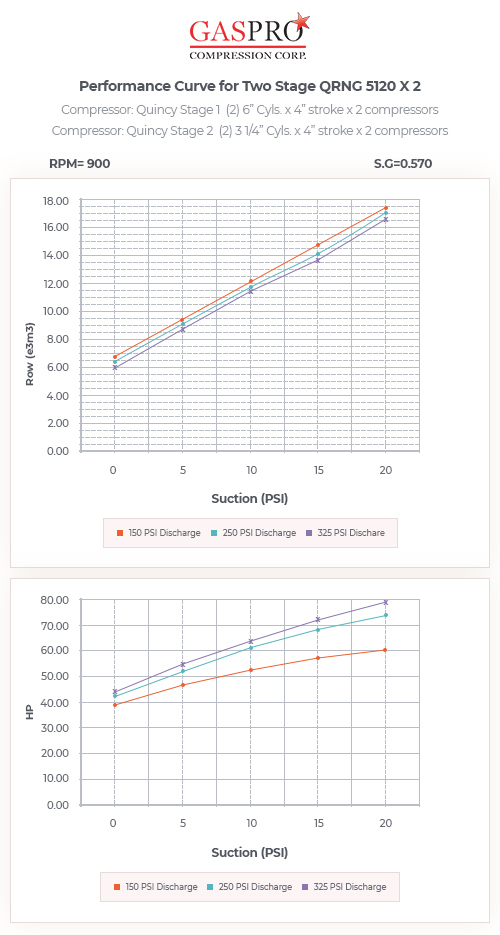
80 BHP – Two Stage
Quincy Compressor
Make: Quincy
Model: QRNG 5120 x 2
Type: Reciprocating
Min / Max Speed: 400-940 RPM
Suction: 0 psi – 20 psi
Max Discharge: 325 psi
Flow: 6.0 e3m3/d – 17.4 e3m3/d
Features of Two-Stage Reciprocating Compressors
A two-stage reciprocating compressor is a mechanical device designed to increase the pressure of a gas by reducing its volume through a series of stages. This type of compressor is commonly used in various industrial applications where high-pressure air or gas is required, such as in refrigeration, air conditioning, natural gas processing, and petrochemical plants.
The operation of a two-stage reciprocating compressor involves two distinct compression stages, each with its own cylinder and piston assembly. In the first stage, the gas is initially compressed to an intermediate pressure by the first piston as it moves through its stroke. The compressed gas then passes through an intercooler, where its temperature is reduced before entering the second stage.
In the second stage, the partially compressed gas from the first stage is further compressed to the desired final pressure by another piston in a separate cylinder. By dividing the compression process into 2 stages, the compressor can achieve higher overall efficiency and lower discharge temperatures compared to single-stage compressors. Additionally, the intercooling between stages helps to reduce the workload on the second stage, improving its efficiency and longevity.
Advantages of Buying a 2-Stage Reciprocating Compressor
Two-stage reciprocating compressors are known for their robustness, reliability, and ability to handle a wide range of operating conditions. They are often preferred in applications where consistent high-pressure output is required, as they can deliver higher pressures than single-stage compressors without excessive heat buildup or mechanical stress.
Maintenance and proper lubrication are essential for ensuring the smooth operation and longevity of a two-stage reciprocating compressor. Regular inspections, oil changes, and component replacements are necessary to prevent wear and tear and minimize the risk of downtime or equipment failure.
In summary, the two-stage reciprocating compressor is a versatile and efficient solution for applications requiring high-pressure gas compression. Its dual-stage design, coupled with intercooling between stages, allows for optimal performance, reliability, and longevity in demanding industrial environments.
How to Choose a Two-Stage Reciprocating Compressor in Alberta?
Choosing the right two-stage reciprocating compressor involves considering several key factors to ensure it meets your specific needs and operating requirements. Here are some essential steps to guide you through the selection process:
Determine required capacity. Calculate the maximum compressed air or gas flow rate (in cubic feet per minute or CFM) needed for your application.
Identify operating pressure. Determine the maximum pressure (in pounds per square inch or PSI) required for your application. Ensure the compressor’s maximum discharge pressure exceeds your operating pressure needs to avoid overloading the system.
Consider the duty cycle. Assess whether your application requires continuous or intermittent operation. Choose a compressor with a duty cycle rating that matches your operating requirements to prevent overheating and premature wear.
Evaluate power source. Determine the available power source (electric, gasoline, diesel) and voltage requirements at your facility. Select a compressor that matches your power source and can operate efficiently within your electrical system’s capacity.
Assess environmental conditions. Consider the ambient temperature, humidity levels, altitude, and any potential exposure to corrosive or hazardous environments. Choose a compressor with suitable cooling and filtration systems to ensure reliable performance in your specific operating conditions.
Evaluate space constraints. Determine the available space for installation and consider the compressor’s footprint, clearance requirements, and ventilation needs. Ensure adequate space for maintenance access and airflow to prevent overheating.
Consider noise level. Evaluate the compressor’s noise level (measured in decibels or dB) and ensure compliance with local regulations and noise ordinances. Select a compressor with sound-dampening features or consider installing noise-reducing enclosures if noise is a concern.
Review maintenance requirements. Assess the manufacturer’s recommended maintenance schedule, including oil changes, filter replacements, and routine inspections. Choose a compressor with accessible components and easy maintenance procedures to minimize downtime and operating costs.
Compare energy efficiency. Evaluate the compressor’s energy consumption and efficiency ratings, such as the CFM per horsepower (CFM/HP) or the compressor’s specific power consumption (kW/CFM). Select a compressor with high-efficiency components and advanced control systems to reduce energy costs and environmental impact.
By carefully considering these factors and consulting with a qualified compressor supplier or technician, you can select the right two-stage reciprocating compressor to meet your specific needs and achieve optimal performance and reliability in your application.
Where to Buy a 2-Stage Reciprocating Compressor in Alberta?
At GasPro Compression, you can purchase quality two-stage reciprocating compressors. We offer long-life reciprocating compressors with economical and reliable motors. They are simple, efficient, and low maintenance. One of the main advantages of the two-stage reciprocating compressors that GasPro Compression sells in Alberta is complete noise isolation.
With us, you can order 2-stage reciprocating compressors from Quincy at an affordable price.
Have questions about two-stage reciprocating compressors? Contact Gas Pro Compression Corporation specialists 403-443-8886 or request a proposal.