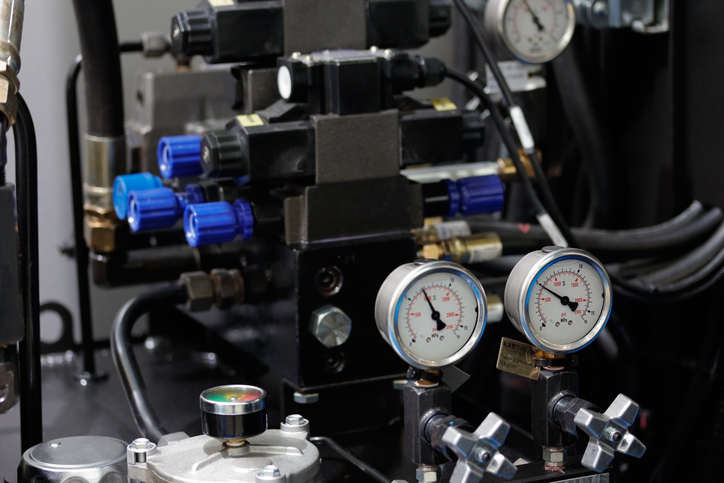
In the oil and gas sector, gas compressor stations are pivotal in ensuring the efficient transportation of natural gas from extraction sites to processing facilities and end-users. These stations employ high-powered compressors to elevate the gas to the required pressure, facilitating its continuous and efficient movement across extensive pipeline networks.
This article delves into the intricacies of how a gas compressor station operates, its essential components, and the various types of compressor stations utilized in the industry.
Defining a Gas Compression Station
A gas compression station is a facility designed to stabilize the flow and pressure of gases within a pipeline network, maintaining optimal levels to maximize carrying capacity. By efficiently collecting gas, re-pressurizing it, and directing it to subsequent processes, these stations ensure the seamless delivery of natural gas to its final destinations.
Key Components of a Gas Compression Station
Understanding how a gas compressor station works involves examining its various components, each contributing to the station’s overall functionality:
- Gas Cooling System: Compressing gas inherently increases its temperature. To prevent potential pipeline damage due to elevated temperatures, compressor stations incorporate cooling systems that lower the gas temperature post-compression.
- Scrubbers and Filters: Before compression, natural gas may contain impurities such as dirt, particulate contaminants, water vapor, and hydrocarbons. Scrubbers and filters are employed to remove these impurities, ensuring the gas is clean and suitable for compression and transportation.
- Condensate Gathering System: This system collects condensates extracted by the scrubbers and injects them back into the gas discharge pipeline using a sparger, ensuring homogeneous propagation of the gas mixture.
- Compressors: At the heart of the station, compressors increase the gas pressure to the desired levels. Depending on specific requirements, a station may house one or multiple compressors, which can be gas turbine-driven, electric motor-driven, engine-driven, reciprocating, or centrifugal types.
- Gas Manifold or Distribution Header: This component distributes the incoming gas to various compressor trains within the station, facilitating organized and efficient processing.
- Corrosion Inhibitor Injector: To mitigate corrosion issues within the equipment and pipeline, a corrosion inhibitor is injected via a dosing pump and tank, prolonging the lifespan of the infrastructure.
- Metering Station: Accurate measurement of gas flow is crucial. Metering stations quantify the gas in standard cubic feet or cubic meters, ensuring precise monitoring and control.
- Utilities: Additional systems such as fire-fighting equipment and instrument air systems are integral to most gas compression stations, enhancing safety and operational efficiency.
Operational Workflow of a Gas Compressor Station
To comprehend how a gas compressor station works, it’s essential to follow the gas’s journey through the facility:
- Inlet and Initial Filtration: Natural gas enters the compressor station and passes through scrubbers that remove condensates and liquids, ensuring the gas is free from impurities that could hinder the compression process.
- Compression Process: The purified gas is directed through an inlet header to the compressor trains. Depending on the required compression levels, the gas may undergo one or two stages of compression.
- Corrosion Inhibition: A corrosion-inhibiting chemical is injected into the gas stream to protect the pipeline and equipment from corrosive damage.
- Cooling Stage: Post-compression, the gas’s temperature is elevated. Air fans in the gas cooler reduce the gas temperature to suitable levels, preventing potential damage to downstream pipelines and equipment.
- Final Filtration and Dehydration: A discharge scrubber separates any remaining liquids from the compressed gas. The gas then enters a dehydration unit to remove any residual moisture, ensuring it meets the required specifications before being sent downstream.
- Delivery: The processed and compressed gas is then transmitted downstream to processing facilities or directly to end-users, depending on the pipeline network’s configuration.
Types of Compressor Stations
There are primarily two types of gas compressor stations, each utilizing different mechanisms to pressurize and transport gas over long distances:
- Reciprocating Compressor Stations: In these stations, gas is drawn into a cylinder where a piston compresses it. Valves ensure that the gas flows in a single direction, facilitating efficient compression. This type is typically used for smaller pipelines or where variable flow rates are required.
- Centrifugal Compressor Stations: These stations utilize spinning impellers to draw gas through a shaft, forcing it through the pipeline. Centrifugal compressors are generally employed for larger pipelines due to their ability to handle substantial gas volumes and provide steady flow rates.
Safety and Environmental Considerations
Understanding how a gas compressor station works also involves recognizing the safety and environmental protocols in place:
- Emergency Shutdown Systems (ESD): Compressor stations are equipped with ESD systems capable of halting operations during emergencies. These systems can block gas flow into the station and safely vent gas from the station piping, minimizing potential hazards.
- Pressure Relief Devices: To prevent over-pressurization, stations are fitted with pressure relief devices that release gas if pressures exceed safe operating limits, ensuring the integrity of the pipeline and equipment.
- Environmental Controls: Modern compressor stations implement measures to minimize environmental impact, including emission control systems to reduce greenhouse gas emissions and noise reduction technologies to mitigate sound pollution.
Advancements in Compressor Station Technology
The evolution of gas compressor stations has led to significant technological advancements aimed at enhancing efficiency, safety, and environmental sustainability:
- Automated Control Systems: Contemporary stations employ sophisticated control systems that monitor and adjust operations in real time, optimizing performance and responding swiftly to changing conditions.
- Predictive Maintenance: Utilizing sensors and data analytics, stations can predict equipment wear and schedule maintenance proactively, reducing downtime and preventing failures.
- Energy Efficiency Improvements: Innovations such as waste heat recovery systems and advanced compressor designs have led to more energy-efficient operations, reducing the carbon footprint of gas transportation.
The Importance of Regular Maintenance
Maintaining the efficiency and reliability of a gas compressor station is crucial to ensuring smooth operations and preventing costly downtimes. Routine maintenance practices play a significant role in extending the lifespan of the equipment and ensuring the safety of the facility. Below are key maintenance activities performed at compressor stations:
- Routine Inspections: Operators conduct regular visual and technical inspections to detect leaks, wear and tear, and abnormal vibrations in compressors and pipelines.
- Lubrication of Moving Parts: Compressors have various moving parts that require proper lubrication to reduce friction and prevent overheating.
- Filter and Scrubber Cleaning: To maintain the purity of the gas, filters, and scrubbers must be cleaned or replaced periodically to prevent blockages.
- Pressure and Temperature Monitoring: Continuous monitoring ensures that the gas pressure and temperature remain within safe and efficient operating limits.
- Vibration Analysis: Advanced sensors monitor the vibration of compressor units, identifying potential faults before they result in major failures.
- Emergency System Checks: Fire suppression systems, emergency shutdown mechanisms, and pressure relief valves are tested to ensure they function correctly in case of an emergency.
By implementing a rigorous maintenance schedule, gas compressor stations can avoid operational disruptions and enhance overall efficiency.
Challenges in Operating a Gas Compressor Station
Understanding how a gas compressor station works also requires an awareness of the challenges that can arise during operation. Some of the most common issues include:
- Pipeline Corrosion: Despite the use of corrosion inhibitors, pipelines and compressors can still experience corrosion over time, leading to structural weaknesses.
- Gas Leaks: Even minor leaks can be hazardous, leading to environmental concerns and operational inefficiencies.
- Compressor Malfunctions: Mechanical failures, overheating, and pressure irregularities can impact the station’s ability to maintain consistent gas flow.
- Fluctuating Gas Demand: Variations in consumer demand can result in inconsistent pressure requirements, requiring adaptive operational strategies.
- Regulatory Compliance: Gas compressor stations must adhere to stringent environmental and safety regulations, which can require frequent upgrades to equipment and processes.
Addressing these challenges effectively requires continuous monitoring, advanced predictive maintenance, and compliance with industry best practices.
Future of Gas Compressor Stations
As technology continues to advance, the future of how a gas compressor station works is expected to evolve with increased efficiency, automation, and environmental sustainability. Some key trends shaping the future include:
- Integration of Renewable Energy: Hybrid gas compressor stations incorporating renewable energy sources like solar and wind power are being developed to reduce reliance on fossil fuels.
- AI-Driven Monitoring Systems: Artificial intelligence (AI) is playing a larger role in predictive maintenance, optimizing operations, and reducing downtime through automated fault detection.
- Improved Emission Controls: Next-generation compressor stations are implementing low-emission turbines and carbon capture technologies to minimize environmental impact.
- Smart Pipelines: Advanced sensors and real-time data analytics are enhancing the monitoring of gas flow, pressure, and temperature, ensuring proactive problem-solving.
So, how does a gas compressor station work in an environmentally responsible way? Modern advancements have led to the development of more energy-efficient compressors, advanced emission control systems, and noise reduction technologies.
These innovations help reduce greenhouse gas emissions and minimize the station’s overall environmental footprint. With these advancements, gas compressor stations will continue to play a vital role in energy transportation while minimizing environmental impact.
How GasPro Can Assist?
GasPro, a leading provider of gas compressor solutions, specializes in high-quality, low-maintenance compressor packages that exceed industry standards. Our team is dedicated to helping businesses optimize their gas transportation systems with:
- Custom-Built Compressor Packages: Designed to meet specific operational needs, ensuring maximum efficiency and durability.
- Compressor System Modifications: Upgrading existing compressor units to enhance performance and reduce energy consumption.
- Comprehensive Maintenance Services: Offering routine maintenance, troubleshooting, and emergency repairs to ensure seamless operations.
- Spare Parts and Components: Providing high-quality compressor parts to extend the longevity of existing equipment.
If you need assistance with designing, modifying, or maintaining a gas compressor station, contact GasPro today to learn more about our solutions.
Conclusion
Understanding how a gas compressor station works is essential for professionals in the oil and gas industry. These facilities play a crucial role in maintaining the steady flow of natural gas through pipelines, ensuring that it reaches processing plants and end-users efficiently. By utilizing high-powered compressors, filtration systems, and advanced monitoring technologies, gas compressor stations optimize the transportation of natural gas across vast distances.
With innovations in automation, energy efficiency, and environmental compliance, the future of how a gas compressor station works is evolving rapidly. As these advancements continue, the industry will benefit from safer, more efficient, and environmentally friendly gas transportation systems.
For businesses seeking reliable compressor solutions, GasPro remains a trusted partner, providing cutting-edge compressor packages, maintenance, and expert consultation. Contact us today to discover how we can help optimize your gas compression operations. Our contact phone number is 403-443-8886.